Guide to 3D Printed Jigs and Fixtures
Jigs and fixtures play a significant role in establishing an ultra-strong foundation within the manufacturing processes. They contribute a lot towards productivity, the safety of the workers, and the reduction of costs incurred. Jigs are guiding tools that enable machining accuracy, like drill jigs, which direct a drill bit to a precisely calculated position in the automotive assemblies. Fixtures are meant to hold workpieces securely while operations such as welding or milling take place.
3D printing has transformed the manufacturing industry by enabling rapid production, massive customization, and significant cost reductions. This guide aims to explain how 3D printing adds value to jig and fixture manufacturing and optimizes the design for best practices.
What Are Jigs and Fixtures?
Difference Between Jigs and Fixtures
- Guiding: If you wonder what jigs are, they guide cutting or drilling tools to their precise positions, thus ensuring accuracy and consistency in different workpieces. For example, a drill jig has bushings that guide different drill bits to specific locations on a workpiece while maintaining position and alignment tolerances between the holes.
- Holding: Fixtures are devices that maintain and support workpieces during manufacturing operations in a secure manner. Unlike jigs, fixtures do not guide tools; they simply fix a workpiece in a defined position. A common example is a welding fixture that accurately aligns components during welding.
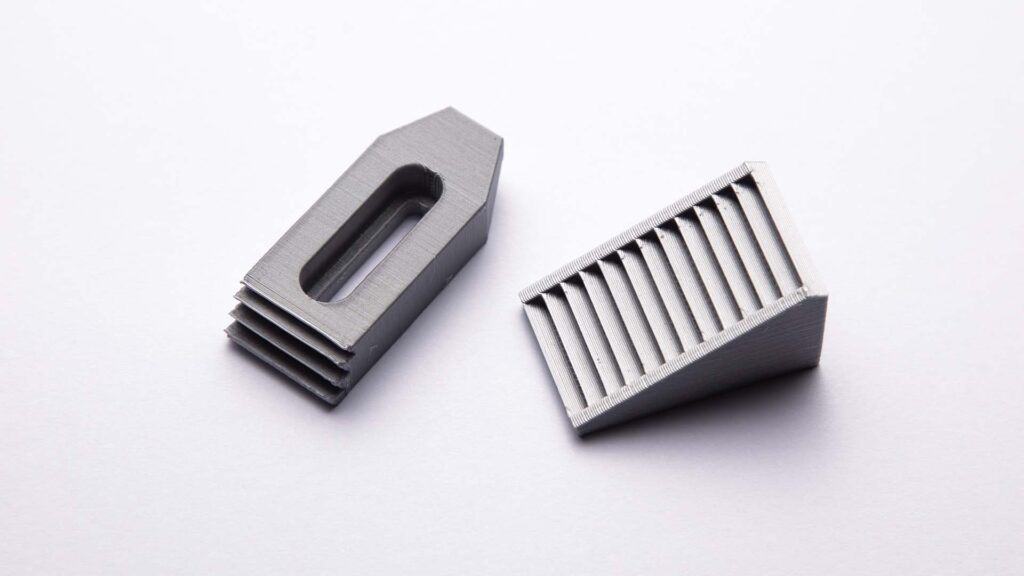
Types of Jigs and Fixtures
There are several types of jigs and fixtures used in 3D printing:
- Assembly Jigs
Straight up, assembly jigs help to align and position accurately components or parts during fastening and welding processes used in production so that it is appropriately defined and sturdy positioned. For example, in automotive assembly, jigs work to align body panels on cars for installation; hence, one can enhance the efficiency and quality of the product as well as assembly.
- Bonding Jigs
Bonding jigs securely hold parts together while adhesives or bonding agents cure, ensuring strong and uniform joints. They apply consistent pressure and maintain precise alignment, making them essential in industries requiring durable and reliable bonds. For instance, a 3d printed woodworking jig helps laminate curved surfaces and ensures consistent bonding in custom furniture.
- Inspection Fixtures
The inspection fixtures hold the components in place very tightly, allowing the inspectors to measure dimensions, geometry, and surface quality. Using 3D printed fixtures suited to specific components would lead to a more effective analysis of the faults detected in the inspection process.
- CNC Tooling
CNC tooling includes cutting tools and fixtures used in CNC machines for precision manufacturing. 3D printed jigs and fixtures like clamps and vises secure workpieces, ensuring stability and accuracy. 3D printing enables cost-effective, custom tooling for enhanced efficiency.
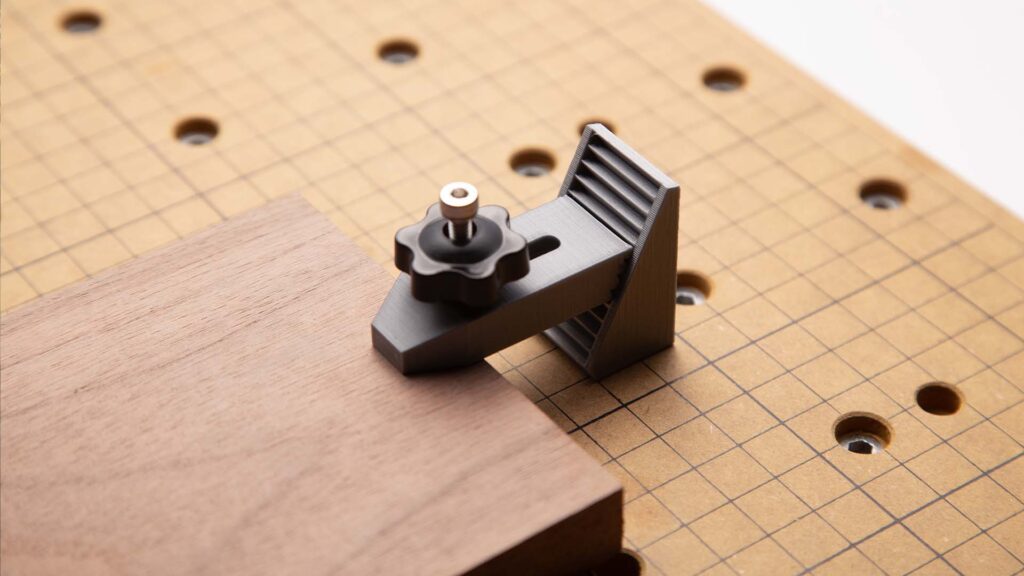
Advantages of 3D Printed Jigs and Fixtures
Cost Reduction
Traditional machining of jigs and fixtures often requires significant investment in materials and machining time. 3D printing dramatically reduces these costs:
- Material usage optimization through generative design
- Elimination of expensive machining operations
- Reduced labor costs in tool production
Time Savings
The transition from design to implementation is significantly compressed:
- Direct CAD-to-print workflow
- Rapid iteration and design optimization
- Typical lead time reduction from weeks to hours
- On-demand replacement part printing
Design Freedom
3D printing enables complex geometries that would be impossible or prohibitively expensive with traditional manufacturing:
- Integrated cooling channels
- Organic shapes for ergonomic handling
- Weight reduction through internal lattice structures
- Custom features for specific applications
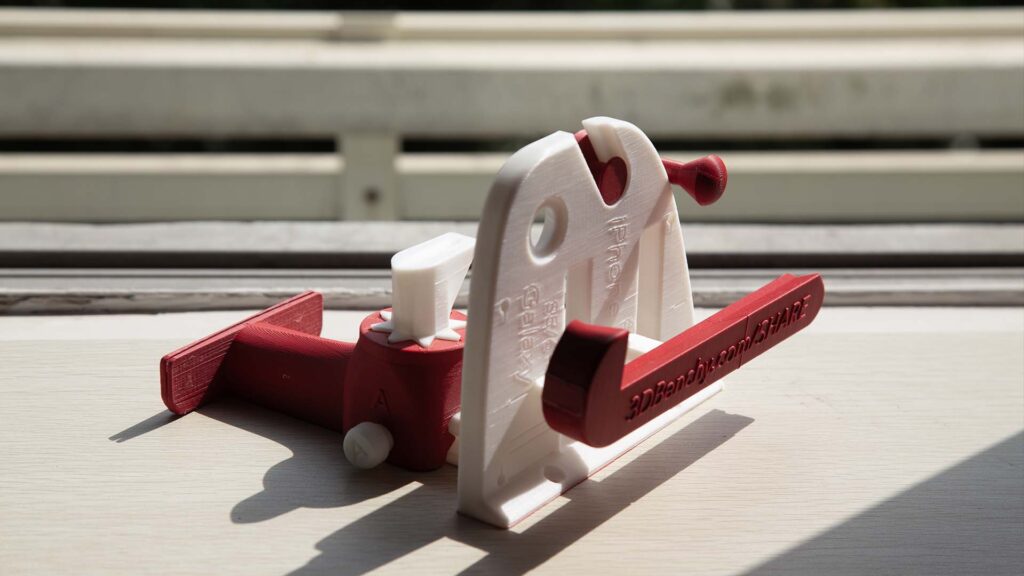
Best Practices: Simple Jig and Fixture Design
Integrated Clamping & Fastening Mechanisms
Incorporating clamps, screws, or slots directly into 3D-printed designs minimizes the need for additional hardware. This approach enhances structural integrity, reduces part count, and simplifies assembly.
Community Resource Recommendation: While not everyone has the time to design and refine their own tools from scratch, many skilled makers have generously shared their tool models in public repositories. r/3dPrintsintheShop is an excellent Reddit community where you can find a wealth of inspiration and designs for 3D-printed workshop tools, jigs, and fixtures. Browsing this community can help you quickly get started, understand the design ideas of other creators, and even directly find ready-made models suitable for your needs, saving significant design time.
Design for Layer Adhesion Strength
The orientation of a print significantly affects its durability. Ensuring that layers align with the primary load direction minimizes weak points, especially in high-stress applications. Proper adhesion improves overall performance and longevity.
Incorporate Chamfers and Fillets to Reduce Stress Concentrations
Sharp edges act as stress concentration points that can lead to fractures. Adding chamfers or fillets helps distribute stress evenly, reinforcing the part and enhancing its durability under load.
Sharp edges are points of concentration of stresses, which can lead to fractures. Chamfering or filleting sharp edges helps to disperse and distribute the stresses evenly, strengthening the part and increasing the life of the component.
Optimize Wall Thickness for Required Rigidity
Wall thickness influences strength and print efficiency. Instead of relying solely on infill density, increasing the number of shell layers often provides better rigidity while maintaining print speed and material efficiency.
Include Reinforcement Ribs in High-stress Areas
Reinforcement ribs can significantly improve the strength and rigidity of parts in specific directions without substantially increasing overall wall thickness, thereby saving material.
Design Principles of Reinforcement Ribs:
- Location: Reinforcement ribs should be present in high-stressed areas of the component or prone to bending.
- Shape and Direction: To achieve optimum performance, the shape and direction of reinforcement ribs shall be consistent with the direction of the load. Typical shapes are triangles, rectangles, and others.
- Connection to Walls: Reinforcement ribs should be well-connected to the walls of the part to effectively transfer stress.
Choosing the Right Filament Material
What is the best filament for jigs and fixtures?
High-Performance (High Strength & Heat Resistance):
- PA+CF (Nylon + Carbon Fiber): PA+CF is high-strength, stiff, and thermal-resistant nylon (polyamide) reinforced with carbon fibers. Printing is relatively easy with very low warpage. It has very good capability in the Z-axis and could be used in industries for withstanding temperatures up to 150°C. Therefore, PA+CF is perfect for all aerospace, automotive, and other demanding applications.
- PC+CF (polycarbonate + carbon fiber): Combining the impact strength of polycarbonate with carbon properties, this composite is ideal for 3D printing components stressed at high value for jigs and fixtures. It’s extremely durable, making it ideal for high-demand industries such as those in automotive and aeronautical fields.
Industrial Strength & Impact Resistance:
- ABS+CF (ABS + Carbon Fiber): ABS+CF enhances traditional ABS with carbon fiber for added strength and rigidity. Lightweight and impact-resistant, it’s ideal for assembly line jigs, fixtures, and high-use parts. It’s suitable for indoor use and is quite affordable compared to PC+CF and PA+CF.
General Purpose & Prototyping:
- PLA (Polylactic Acid): Easy to print but not very durable or heat-resistant; best for prototypes.
- PETG: Durable, chemical-resistant, and easy to print, making it a versatile choice.
Printing Parameters
Note: This data is intended for general understanding only. For more in-depth and nuanced information, it is recommended to consult detailed engineering resources and material datasheets, and to test and iterate designs based on specific application requirements.
Parameter | Jigs | Fixtures |
Layer Height | 0.2mm | 0.15-0.2mm |
Infill | 50% gyroid | 80% rectilinear |
Walls | 3 layers | 4 layers + ribs |
Brim | Required for PA/PC | Optional for PETG |
Final Words
3D printing has transformed jig and fixture production, making it more accessible, cost-effective, and customizable. Manufacturers can achieve high-performance, durable tools tailored to their needs by leveraging the right design principles and materials.