History of CNC Machines: From Punch Cards to Your Desktop
Today, CNC machines are a mainstay for manufacturing and production, ensuring precision and efficiency. But how did they emerge and become one of the most fundamental components in production? We will delve deeper into their history, learn about what is CNC system, and also highlight different types of CNC machines.
Table of Contents
- From Numerical Control to the First CNC Machine
- The Birth of CNC
- The Rise of Desktop CNC
- Key Moments in Desktop CNC History
- Types of Desktop CNC Machines
- Conclusion
From Numerical Control to the First CNC Machine
The backbone of any desktop CNC is actually founded on Numerical Control (NC). But what does CNC stand for? It stands for Computerized Numerical Control, which, to begin with, developed from the need for more precision in manufacturing and more automation in the manufacturing of intricate parts, especially from the aerospace industries. All of these factors were taken into account in the development process of NC in the late 1940s and early 1950s.
The conventional, accepted “first” CNC machine was, however, a hydro-mechanical milling machine built at the Massachusetts Institute of Technology during the late 1940s and early 1950s under a contract from the US Air Force. John T. Parsons led the project, recognizing the possibility of punched cards being used to input coordinate data for controlling the movements of a machine tool.
To put it in the simplest terms:
- The problem with manufacturing involves very complex three-dimensional aircraft parts (as with the rotor blades of helicopters) needing to be produced with accuracy, and this type of work was also often laborious and erratic by manual methods.
- Parsons’ concept: He thought of putting a system in place under which numerical data punched on cards would control the movement of the machine.
- MIT Collaboration: Parsons worked with MIT’s Servomechanisms Laboratory to develop this notion.
- The First CNC Machine: This resulted in a modified milling machine that directed the movement of servomotors connected with signals read from punched cards along three axes, defining the position of the cutting tool. This demonstrated the feasibility of computer-controlled machining.
While this groundbreaking machine was not a computer in the modern sense, it laid the groundwork for Computer Numerical Control. The “computer” aspect came later with the integrating of actual computers into the control systems.
The Birth of CNC
The true revolution came with the integration of computers into the control systems. The first step was crossing from NC to Computer Numerical Control (CNC). Very huge, expensive, and mainly used within large industrial installations were the early CNC machines, when one thought of a “CNC machine”; it conjured images of great, gigantic milling machines and lathes in factories.
The Rise of Desktop CNC
It was not until decades later that the dream of CNC coming into the small shop, school, or even home became a reality. Several developments in technology paved the way for desktop CNC machines:
- Miniaturization of Computing, as smaller, more powerful, and less expensive computers came along, making it feasible to include them in smaller machine tools.
- Microcontroller Revolution: All machine tools have spread low-cost and compact control systems with the introduction of microcontrollers.
- Better motor technology: Smaller, more precise stepper and servo motors enabled accurate control of movement in smaller form factors.
- The Maker Movement: There is growing interest in personal fabrication and DIY businesses, fueling demand for widely available CNC tools.
Key Moments in Desktop CNC History
- Late 20th Century
- Early 2000s
- Mid to Late 2000s
- 2010s and Beyond
Towards the end of the 20th century: Early in the 21st century, small kit-type CNC machines started pouring in for hobbyists and educational purposes. Such machines were often the poor cousins of machines in the industrial setting. “CNC” would be a largely industrialized concept.
Into the early 2000s: The propagation of open source, through RepRap and other projects, was a defining element in opening up CNC technology: Although RepRap was about 3D printing, its principles of open-source hardware and software were applied to low-cost control systems for other kinds of CNC machines, thereby doing much to popularize CNC. The association of “CNC” with anything that wasn’t a subtractive tool began.
More likely Mid to Late 2000s: This change saw desktop CNC routers hitting the market at reasonable prices with desktop CNC mills becoming even better affordable. These soon enabled the maker, and small business, to dabble in wood, plastics, and even light metals. The whole language now saw evolution, where “desktop” was prefixed to create a distinction between these smaller machines.
2010s and Beyond: The market for desktop CNC machines truly exploded. Desktop CNC laser cutters bring forth fine cutting and engraving. Importantly, desktop CNC 3D printers also get their fair share of falling prices. The understanding of “CNC machine” hence becomes very broad: not only machining, but also additive methods can fall into the same definition. New terminologies began to arise, giving rise to common terms such as CNC router, CNC mill, CNC laser cutter, and CNC 3D printer.
The latest era also saw the emergence of versatile machines like the Artisan 3-in-1, which integrates 3D printing, laser engraving/cutting, and powerful CNC machining into a single unit. The Artisan comes standard with a robust 200W CNC module that machines challenging materials, including beech, walnut, and jade.
Types of Desktop CNC Machines
- Desktop CNC Routers: Ideal for carving, cutting, and shaping wood, plastics, and composites. They represent a continuation of the traditional subtractive CNC concept in a smaller form factor.
- Desktop CNC Mills: capable of removing material on metals and tougher plastics with absolute precision at a smaller scale so as to bring industrial milling capabilities at a very small scale.
- Desktop CNC Laser Cutters: Offer cutting and engraving capabilities on a wide range of substrates with precision cuts and engravings using a focused laser beam. This introduced a different method of material removal under CNC.
- Desktop CNC 3D Printers: As discussed earlier, these additive machines build objects layer by layer from digital designs. Their inclusion significantly expanded the definition of a “CNC machine” to include additive processes.
Furthermore, the capabilities of desktop CNC machining can be expanded with the addition of a rotary module. For Artisan 3-in-1, the rotary module upgrades the standard 3-axis CNC to a 4-axis system, enabling 360° rotation of the workpiece. This allows the creation of intricate three-dimensional shapes that are difficult to achieve with a standard 3-axis setup.
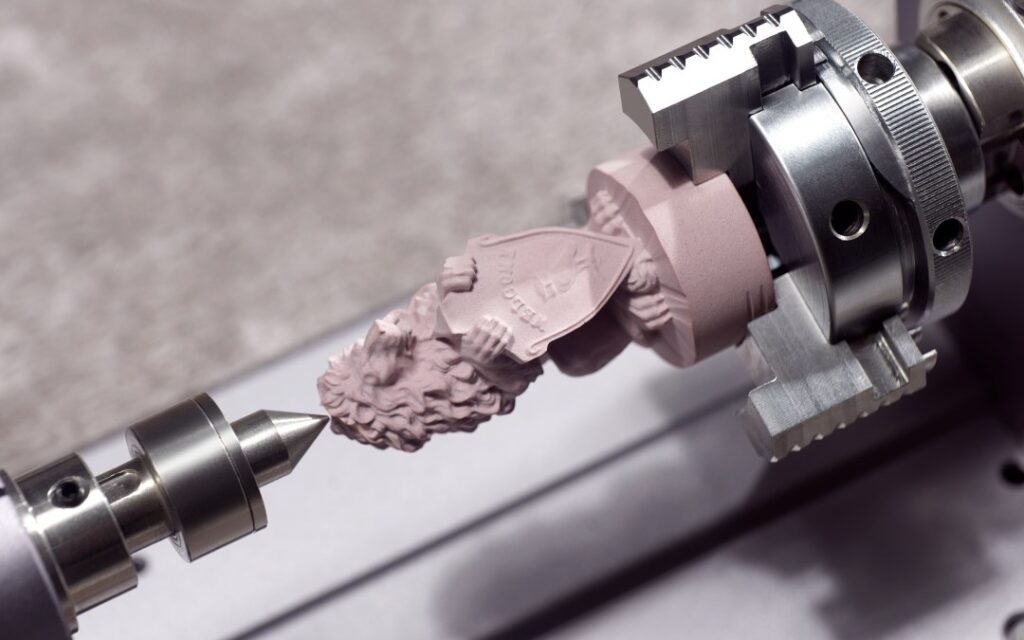
As the types of CNC machines have diversified, so has our language around them. Initially, “CNC machine” almost exclusively referred to large, subtractive tools. However, with the advent of desktop versions and the rise of additive manufacturing, we now commonly use more specific terms to avoid ambiguity. The prefix “desktop” clearly indicates a smaller, more accessible machine. Furthermore, specifying the type of process (routing, milling, laser cutting, 3D printing) provides a clearer understanding of the machine’s function.
Conclusion
By deepening into the history of CNC machines, we get to know the marvelous journey of invention and to discover CNC technology for itself, it is not just the processing of materials but how it is also applied in other sectors like aerospace, automotive, and healthcare in the endeavor to bring quality and innovation in the development of products.