Injection Molding vs. 3D Printing: Choosing the Right Path for Your Vision
In the evolving landscape of manufacturing, choosing the right process is paramount. While injection molding and 3D printing are often presented as competing methods, understanding their fundamental differences reveals that they serve distinct purposes and cater to different scales of creation.
This blog post aims to move beyond a simple Injection Molding vs. 3D Printing comparison, offering a deeper insight into the unique value proposition of each, and how versatile tools like our 3-in-1 machines are democratizing creation.
What Is Injection Molding
What is injection molding in simple terms? It’s the process of injecting molten plastic into a mold to create identical parts – a powerhouse for mass-producing plastic components. This traditional method excels at high-volume runs, delivering consistent quality and cost-effectiveness when producing thousands or millions of units. It’s the workhorse of industries needing standardized parts in vast quantities.
Advantages of Injection Molding
- High Volume Production & Cost-Effectiveness at Scale: Unmatched efficiency for mass manufacturing, driving down per-unit costs in large runs.
- Material Variety & Part Consistency: Compatible with numerous plastics, ensuring uniform material properties and consistent quality.
- Fast Cycle Times & Superior Surface Finish: Rapid production cycles with excellent surface finish, minimizing post-processing requirements.
- Precision & Tolerance: Produces components with tight dimensional accuracy and consistent tolerances for engineering applications.
Disadvantages of Injection Molding
- High Upfront Costs & Longer Lead Times: Significant investment in injection molds cost and mold creation leads to longer lead times and higher initial expenses.
- Limited Design Flexibility & Customization: Design changes are costly after mold creation, and complex geometries can increase mold complexity and expense.
- Not Economical for Low Volumes: The high tooling cost makes it less viable for small production runs or prototyping.
What Is 3D Printing
3D printing (additive manufacturing) builds components layer by layer from digital models. This technology is optimal for prototyping, limited production runs, and creating customized or geometrically complex items. It offers design freedom, enabling intricate internal structures and on-demand manufacturing.
Advantages of 3D Printing
- Design Flexibility & Complexity: Enables the creation of highly intricate geometries, customized designs, and complex internal structures with relative ease.
- Rapid Prototyping: Offers fast turnaround times for design iterations and functional prototypes, accelerating product development.
- Low-Volume Production Viability: Economical and efficient for small production runs, customized parts, and bridge manufacturing.
- On-Demand Manufacturing: Parts can be produced as needed, minimizing inventory, waste, and the need for large production batches.
- Material Innovation: Constantly expanding material options, including a growing range of plastics, metals, ceramics, composites, and even specialized materials.
- Tooling-Free Production: Eliminates the need for expensive molds, drastically reducing upfront costs and lead times, especially beneficial for smaller companies and startups.
Disadvantages of 3D Printing
What are the disadvantages of 3D printing? While revolutionary, 3D printing also has limitations:
- Higher Cost per Part (Low Volumes): Generally more expensive per part than injection molding for large volumes.
- Slower Production Speeds: Layer-by-layer construction can be slower than injection molding’s cycle times, especially for larger parts and high volumes.
- Limited Material Selection (Compared to Injection Molding): While material options are growing, the range is still narrower than the vast plastics available for injection molding.
- Surface Finish and Precision: The surface finish can be stepped and may require post-processing. Depending on the 3D printing technology, precision and tolerances can be lower than those of injection molding.
- 3D Printed Injection Molds: Their limited pressure and temperature resistance, moderate accuracy, and reduced durability may challenge their effectiveness in batch production. Traditional metal molds remain superior for precision parts and continuous manufacturing.
3D Printing: Creation for Individuals
Is injection molding better than 3D printing? This question misses the point. It’s like asking if a cargo ship is “better” than a personal sailboat. They serve vastly different purposes. 3D printing isn’t just another manufacturing method; it’s a revolution in access to creation.
The true impact of 3D printing lies in its democratization of design and production. It’s shifting power from centralized factories to individuals, small businesses, and communities.
- Empowering the Individual Designer and Maker:
- Accessible Technology: Affordable and user-friendly, empowering anyone with an idea to become a creator.
- Multi-Functionality: Snapmaker Artisan machine, combining 3D printing with laser engraving and CNC machining, expands design possibilities and material options, offering a comprehensive desktop fabrication studio.
- For Small Businesses & Hobbyists: Startups can launch products with minimal investment, and hobbyists can bring their visions to life with professional-grade tools at home.
- Towards Decentralized and Localized Production:
- Local Production: Reduce reliance on long supply chains and support local economies by producing goods within communities.
- Resilient Supply Chains: Enable local production of essential items during disruptions.
- Maker Communities: Foster local entrepreneurship and creative hubs.
In essence, the 3D printing revolution is about empowering you. It’s about giving individuals the power to design, create, and personalize their world, fostering a new era of distributed innovation and individual expression.
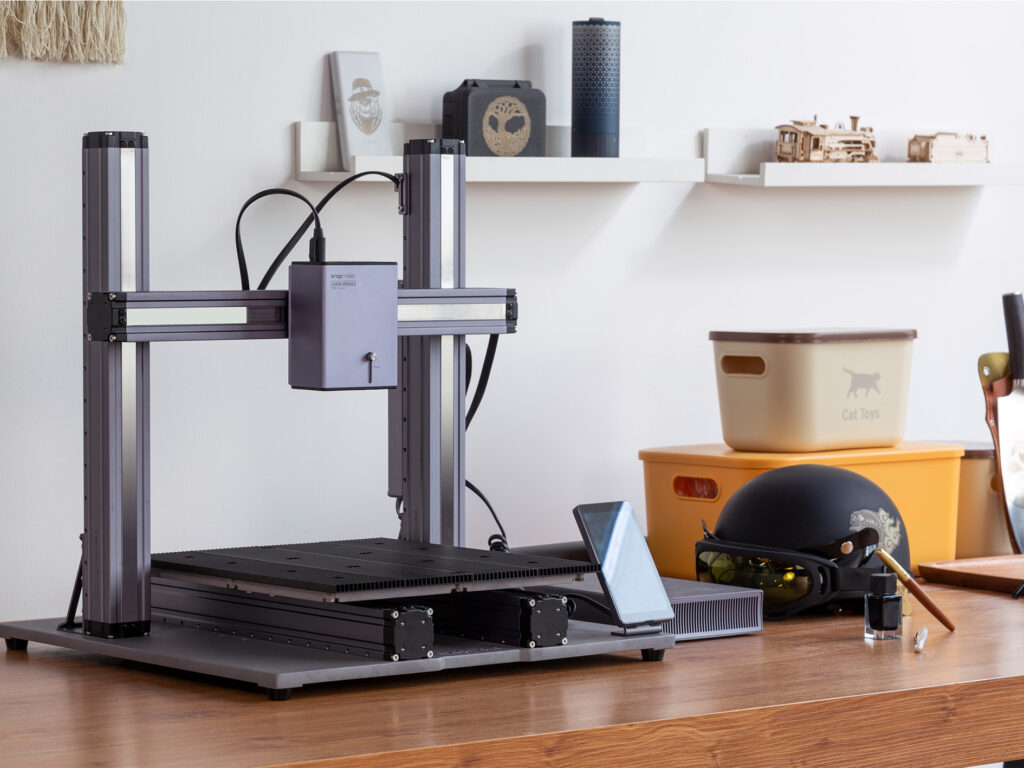
When to Leverage Injection Molding vs. 3D Printing
Choose Injection Molding if:
- Massive Production Runs are Needed: For extremely high volumes, injection molding’s per-unit cost advantage becomes undeniable.
- Finalized Designs and Material Specifications: When designs are locked and material properties are critical and well-defined for a specific plastic.
- Uncompromising Surface Finish and Precision are Mandatory: For applications demanding the absolute smoothest surface and highest dimensional accuracy right off the production line.
Choose 3D Printing if:
- Prototyping and Design Iteration are Key: Quickly test and refine designs with rapid 3D printing capabilities.
- Low to Medium Volume Production is Sufficient: Produce parts cost-effectively in smaller batches, which is perfectly suited for customized products or niche markets.
- Design Complexity and Customization are Paramount: Unlock intricate geometries and easily tailor designs for individual clients or specific needs.
- Rapid Turnaround and Minimal Upfront Costs are Essential: Get parts faster and start projects without the heavy investment of injection molds.
- Exploring Different Materials and Finishes is Desired: Experiment with a range of 3D printing materials and utilize CNC machining for enhanced precision and surface finish on printed parts.
Conclusion
Injection molding and 3D printing are not rivals, but rather complementary forces in the manufacturing world. Injection molding remains essential for mass production, while 3D printing, especially in versatile 3-in-1 machines, is spearheading a revolution in personalized creation and individual empowerment.