Inspiring Ways to Recycle Your 3D Printer Filament
Failed prints, support structures, prototypes destined for the bin, the colorful “poop” purged during multi-color prints – if you’re involved in 3D printing, you likely have a growing collection of filament waste. It’s a common sight in workshops and labs. This often leads to the question: “Is there a way to recycle 3D printer filament?” The encouraging answer is definitely YES.
In this article, we’ll explore different directions for recycling filament waste and discuss common considerations. Taking this article as an insightful starting point for your own projects, rather than exhaustive instructions.
Table of Contents
How to Recycle 3D Printer Filaments
So, how can we turn those piles of plastic into something useful again? There are a few key approaches:
DIY Filament Extruder
For the truly dedicated maker aiming for a circular workflow, creating a DIY filament extruder line is the ultimate goal. This involves transforming your plastic waste directly back into printable filament.
The process requires:
- Sorting: Separate plastics by type (PLA, PETG, etc.) as mixing causes material failures
- Cleaning: Remove all glue, dirt, and contaminants
- Shredding: Break down failed prints and support structures into uniform flakes
- Drying: Remove moisture (typically in a low-temperature oven) to prevent bubble formation
- Extrusion: Feed dried flakes into a desktop extruder where they melt and pass through a precision nozzle
- Cooling and Measuring: Maintain consistent diameter (1.75mm or 2.85mm) using sensors and feedback systems
- Spooling: Wind the cooled filament onto a spool for future use
The process involves mechanical challenges: inconsistent diameters, extruder jams, and unpredictable color blending. It requires significant hardware investment (shredder, dryer, extruder, winder) and understanding of polymer properties.
Mold Casting: Direct Repurposing
A more accessible alternative to filament extrusion is melting scraps for casting into new objects.
- Collection and Sorting: Group plastics by type. Different plastics (PLA, PETG, ABS, etc.) melt at varying temperatures and do not mix well. Sorting plastic types by color is advisable, as this allows you to plan for desired visual effects like swirls or specific color blocks.
- Melting: Heat plastic (PLA is preferred at around 180°C) in a dedicated toaster oven designated solely for melting plastics. This helps prevent toxic residues from contaminating food surfaces. Remember to ensure good ventilation to avoid accumulating VOCs.
- Molding: Carefully pour the thoroughly melted plastic into heat-resistant molds; silicone molds are often ideal due to their flexibility which aids in easy demolding, but clean metal tins or custom-made molds can also be used. Ensure your chosen mold is clean and dry before pouring.
- Cooling and Finishing: Allow the plastic to cool completely within the mold, noting that cooling time will vary significantly depending on the size and thickness of the object. Once fully solidified, you can remove the item, and minor finishing like trimming or sanding rough edges might be needed for a clean look.
This method produces distinctive objects with marbled or terrazzo-like patterns. Common applications include buttons, coasters, pendants, decorative tiles, and small figurines.
For more advanced projects, versatile multi-function machines like the Artisan 3-in-1 offer significant advantages. Using its CNC milling capabilities, you can create precise negative master molds from wood or acrylic. A practical approach often involves using this master to cast a durable, heat-resistant silicone rubber mold, which captures fine details effectively and withstands repeated use with hot plastic. Simultaneously, its laser cutting function allows for adding intricate pattern designs to your molds or parts. This combination is particularly effective for crafting batches of custom buttons from sorted PLA waste—simply design your button, CNC a mold master, cast your silicone production mold, then melt and pour your PLA scraps.
The process requires less technical equipment than filament extrusion, focusing on creative expression rather than precision manufacturing.
Empty Spool Repurposing
What to do with old 3D printer filament spools? The plastic or cardboard spools that hold filament offer additional recycling opportunities:
- Can be converted into storage solutions
- Used as bases for painting projects
- Incorporated into planters
- Repurposed as structural elements for toys or sculptures
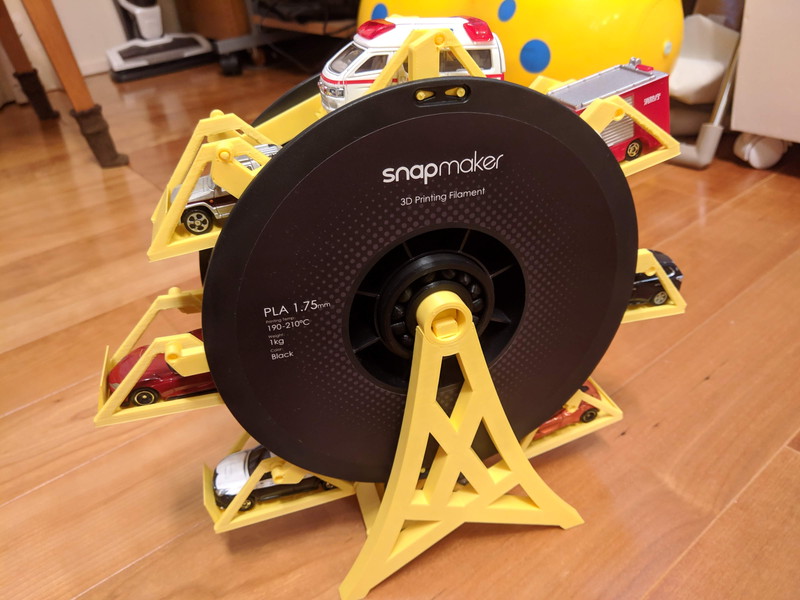
Notable examples include converting spools into Ferris wheel garages for toy cars and creating modular organizational systems.
Is It Worth It to Recycle Filament?
Given the effort involved, especially with DIY extrusion, is it truly worthwhile? The value proposition of filament recycling could be examined from multiple angles:
Environmental Impact
Recycling definitively reduces plastic waste headed to landfills or incineration, representing a significant step toward making 3D printing more sustainable. Learn more in The Environmental Impact of 3D Printing: Is It Sustainable?
Cost-Effectiveness
The economics are nuanced:
- DIY extrusion promises long-term material cost savings but requires substantial initial equipment investment
- Time requirements for processing can be significant
- Energy consumption for shredding, drying, and melting adds to operational costs
- Small-scale hobbyists may not find it economically viable unless viewed as part of a learning process or long-term commitment
- Melting and casting methods offer much lower financial barriers to entry
Community Collaboration
This approach maximizes recycling benefits:
- Equipment for efficient shredding and extrusion is ideal for community use
- Makerspaces, schools, and local 3D printing clubs can pool resources
- Shared equipment makes high-quality recycling accessible and cost-effective
- Collective scraps and knowledge exchange enhance collaboration
Learning & Innovation
Beyond practical considerations, the process itself delivers value by fostering hands-on learning about:
- Materials science
- Engineering principles
- Problem-solving challenges
- Core maker skills and mindset
The recycling journey often extends beyond simple cost calculations to encompass broader benefits to makers and their communities.
Final Words
Filament recycling represents a promising frontier in the 3D printing ecosystem. Whether you choose to:
- Build a complete extrusion system
- Repurpose plastic through melting and casting
- Join community recycling efforts
Each approach contributes to sustainable making practices and reduces waste. DIY recycling methods require adaptation to your specific materials and equipment. Start with methods that match your resources and goals, then expand your capabilities as your experience grows.